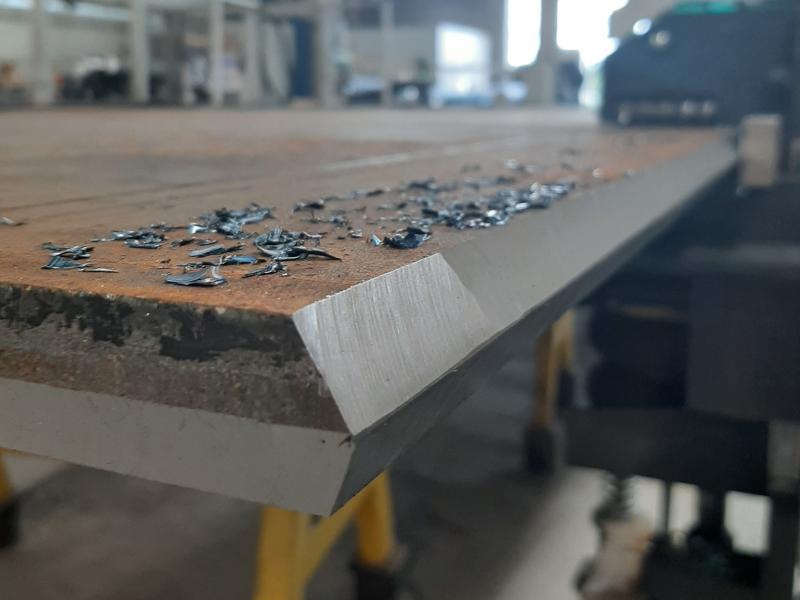
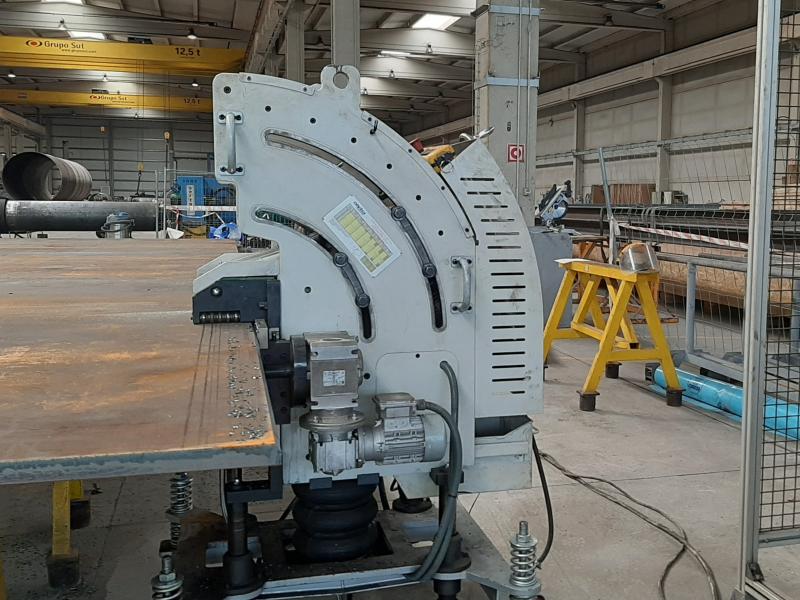
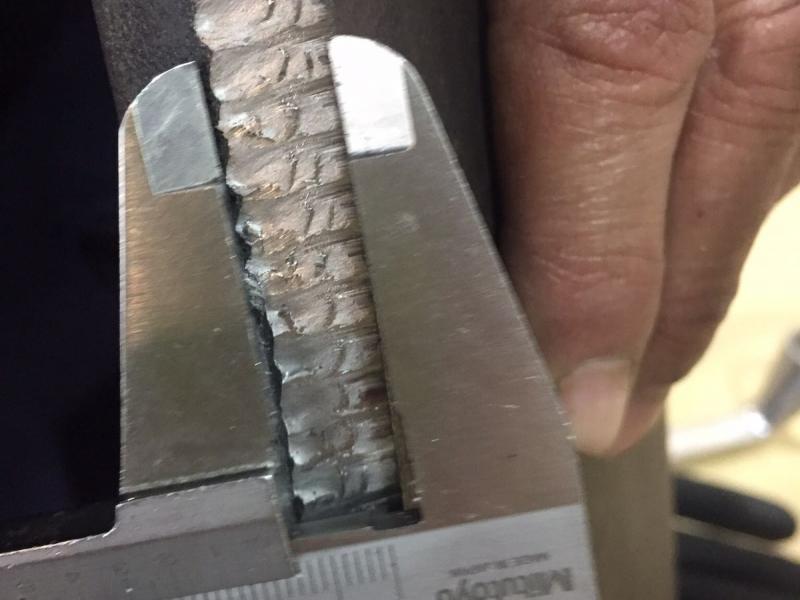
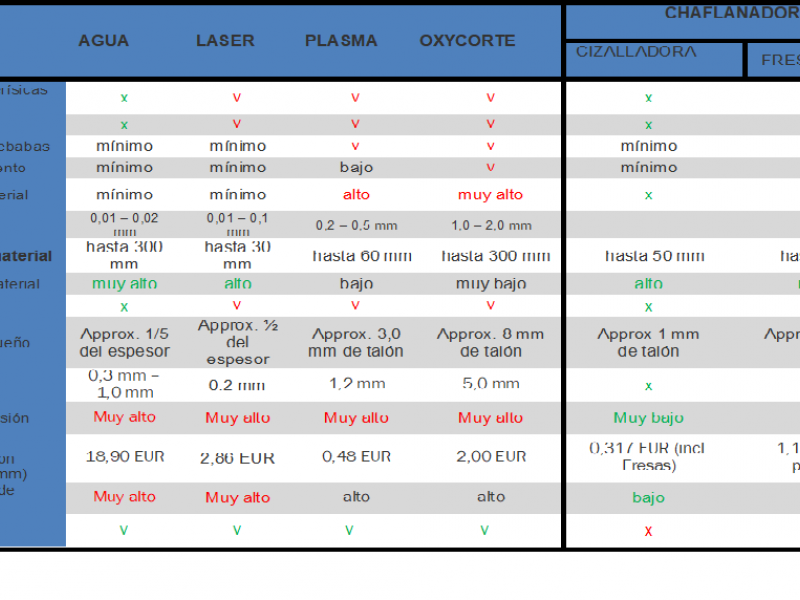
¿Corte con láser, agua o plasma? ¿Un sistema CNC de inversión intensiva que ocupa mucho espacio? En muchos casos la elaboración mecánica de chaflanes es extremadamente útil y de alto interés para muchos usuarios. Los chaflanes de contorno 3D no siempre son necesarios. Muchos usuarios a menudo se enfrentan a la pregunta de qué método es el más rentable para su aplicación, ya que en las ventajas del método de chaflanado dependen los requisitos y el material. Sin embargo, estos procesos no compiten entre sí, sino que forman una alianza significativa en muchos procesos de fabricación.
A continuación explicaremos los métodos de chaflanado más comunes:
• Chaflanado mecánico
• Corte por láser
• Corte por agua
• Corte por plasma
• Resumen
Chaflanado mecánico con fresadoras portátiles y biseladoras por cizalladora
Además de los resultados eficientes y profesionales, una de las principales ventajas de la preparación de soldadura mecanizada es la inocuidad para la salud. En contraste con los métodos comunes de preparación de soldadura, que producen polvo fino o incluso gases tóxicos que entran en el aire y, por lo tanto, pueden inhalarse, el procesamiento mecanizado solo da como resultado virutas más pequeñas en el caso del mecanizado y más gruesas en el cizallado que simplemente caen al suelo o en los contenedores designados para ello.
Para garantizar la mejor calidad de soldaduras los aceites, grasas, barnices, pinturas y capas de óxido en las partes soldadas deben eliminarse para que las juntas en los que se realiza el trabajo estén limpias. Al procesar, también debe asegurarse de que no se utilicen refrigerantes y lubricantes que contengan aceite. La preparación mecanizada de la soldadura evita esto. Con este procedimiento, se prescinde por completo de emulsiones que contienen agua de enfriamiento, que en la mayoría de los casos se usa en la preparación de costuras de soldadura mediante fresadoras manuales o CNC, y en su lugar se mecaniza o se cizalla el material completamente en seco
Fresadora portátil para la elaboración de chaflanes
Las fresadoras móviles están reemplazando cada vez más los procedimientos clásicos para la preparación de soldadura, como las biseladoras por cizallado, el oxicorte y la elaboración manual mediante amoladoras angulares. Las máquinas modernas y potentes no solo garantizan una mayor eficiencia, sino que también impresionan con su alta calidad de superficie. La máquina se mueve a lo largo de la chapa o trabaja en fijo, por lo que su uso es muy flexible, ocupa poco espacio y es muy económico.
Las chaflanadoras muestran sus habilidades, especialmente cuando se utilizan con grandes espesores de chapa. Se pueden usar varios modelos para chaflanes superiores e inferiores, lo que hace innecesario el volteo complejo de chapas.
Procesamiento de bordes con el método de cizallado
La forma más eficiente de la elaboración de chaflanes es con las máquinas de cizallado.
Estas máquinas funcionan con el método cizallado. Aquí, una viruta larga se corta del borde de la chapa mediante una herramienta de corte o fresa que gira. Esto permite velocidades de casi 2,6 m / min (hasta 5 veces más rápido que los métodos convencionales). Los costes para el chaflán son hasta un 75% más bajos que con otros procesos. Sin polvo y sin ruido, ya que no hay polvos ni gases. Un método muy eficaz y económico para la preparación de soldaduras. Las fresas duraderas son ideales para acero y acero inoxidable.
Ventajas y desventajas
Ventajas
- Trabaja espesores de hasta 100 mm.
- Corte de aceros de alta aleación.
- Silencioso
- Alta rentabilidad
- Uso óptimo de los materiales.
- Ancho de corte pequeño
- Sin estrés térmico
- Más seguro para los usuarios y el medio ambiente.
- No requiere procesamiento posterior
- Bajos costes operativos
- Alta velocidad de corte
- Tiempos de set-up muy bajos
- Uso por personal no especializados
- Sin limitación en cuanto a tamaño de pieza
Desventajas
• Acabado final rugoso mediante cizallado
• Alta especialización, no utilizable para otros procesos
• Espesores de material limitados
Características del láser.
El láser ha abierto nuevas aplicaciones en el campo del procesamiento de chapa. En el sector de las de espesores pequeños en particular, no hay forma de evitar el corte por láser debido a las altas velocidades de corte y al bajo estrés térmico. El procesamiento láser impresiona con filos de corte casi a escuadra y un aprovechamiento del material con tolerancias alcanzables de hasta +/- 0.1 mm / m. Una variedad casi ilimitada de materiales ha convertido al láser en el número 1 entre las herramientas de corte en muchas áreas. De forma segura se puede cortar el acero inoxidable de hasta 50 mm, el acero al carbono de hasta 40 mm y el aluminio de hasta 20 mm. Pero los láseres también se usan para trabajar otros tipos de materiales como madera, plástico o papel. La desventaja del corte por láser es la reducción de la estabilidad del proceso con superficies reflectantes, un rango de grosor de chapa limitado y las amplias medidas de seguridad laboral.
Ventajas y desventajas
Ventajas
• Altas velocidades de corte.
• Ausencia de rebabas.
• Baja influencia del calor
• Precisión dimensional perfecta
• Optimó aprovechamiento del material.
• Tiempos de procesamiento cortos
• Brecha mínima de corte
• Gran variedad de materiales.
Desventajas
• Altos costos de inversión
• Espesores de material limitados
• Seguridad laboral integral
• Inestabilidad del proceso con reflejos.
Corte por agua
El corte por agua es una alternativa efectiva a los procesos de corte convencionales y la solución de corte ideal para muchos usuarios. Desde espuma hasta zafiro duro, con un chorro de agua a alta presión de hasta 6.200 bar, incluso los materiales más duros se vuelven tan blandos como la mantequilla. Es sobretodo utilizado con materiales sensibles al calor. Gracias a los últimos desarrollos tecnológicos, este innovador proceso está entrando en nuevas áreas de precisión y productividad. El resultado es una calidad significativamente mejorada de tolerancia de piezas y precisión angular. Al agregar abrasivos de bordes afilados, como arena o cuarzo, la efectividad del corte por agua se puede aumentar nuevamente, por lo que también se pueden cortar espesores de material muy gruesos. Se puede cortar acero inoxidable de hasta 300 mm y aluminio de hasta 400 mm de espesor.
Ventajas y desventajas
Ventajas
• Alta rentabilidad
• Gran variedad de materiales.
• Uso óptimo de los materiales.
• Ancho de corte pequeño
• Sin estrés térmico
• Cortar material grueso
• Alta precisión hasta el rango micro
• Más seguro para los usuarios y el medio ambiente.
• Normalmente no se requiere procesamiento posterior
Desventajas
• Altos costes del proceso
• Gran riesgo de corrosión.
• Velocidad de corte lenta
• Tratamiento del agua de corte.
• Eliminación de los abrasivos.
Corte por plasma
El corte por plasma ha progresado significativamente en los últimos años debido al desarrollo de los últimos quemadores multigás, que es uno de los procesos de separación más económicos, especialmente para chapas gruesas de CrNi y en la gama de acero medio. La calidad de corte en el rango de espesor de 15 mm a 40 mm es la misma que la del corte por láser. Sin embargo, este proceso de separación térmica impresiona con las altas velocidades de corte, por lo que la productividad del proceso de fabricación aumenta significativamente. El corte por plasma ofrece amplias ventajas, particularmente en la producción de componentes que todavía tienen que ser soldados, torneados, fresados o mecanizados en el procesamiento posterior.
Ventajas y desventajas
Ventajas
• Corta todos los materiales conductores.
• Grosores de corte de hasta 200 mm.
• Alta calidad en resistencias medias.
• Corte de aceros de alta aleación.
Desventajas
• Coste elevado de operación
• Brecha de corte relativamente amplia
• Generalmente altos niveles de ruido
• Endurecimiento de las zonas marginales.
• Se requiere procesamiento posterior
Conclusiones de la comparación
¿Cuál es el mejor método de corte?
No hay una respuesta clara a esta pregunta, porque primero debe aclararse qué se entiende por el término "mejor". Y dependiendo de la tarea de corte un método es el más apropiado. Ningún proceso puede considerarse el único correcto, pero todos los procesos de corte tienen sus propiedades, sus áreas especiales de aplicación, fortalezas y debilidades, ventajas y desventajas y estructuras de costes individuales.
Siempre depende de la aplicación y las exigencias del cliente.
¿Cuáles son sus criterios para un buen corte, para el mejor corte?
¿Es el coste de fabricación decisivo?
¿Es la precisión según ISO 9013 de las piezas cortadas?
¿Es la influencia térmica, el cambio estructural en el material?
¿Es la soldabilidad?
¿Es el endurecimiento del material y, por lo tanto, su idoneidad para las clases de ejecución ISO 1090?
¿La calidad del material requiere ciertas reglas de tratamiento?
¿Es muy alto el requisito de geometría para el corte?
¿Qué tratamiento obtiene de la pieza después?
¿Deben pintarse, recubrirse con polvo o galvanizarse?
Por lo tanto, la gran cantidad de criterios hace que sea imposible hacer declaraciones generales. Los requisitos de sus clientes y la eficiencia económica de la producción de chaflanes son importantes.
El corte por láser es siempre la primera opción en el sector de las chapas finas. De esta manera, las piezas de una amplia variedad de grupos de materiales pueden fabricarse con una precisión de componentes muy alta sin reelaboración mecánica.
Para espesores de material superiores a 300 mm, solo el oxicorte y el corte por agua son adecuados. Refiriéndose a la calidad, la decisión de cortar acero por agua es ciertamente lógica, pero no todos los usuarios pueden hacer esta inversión y no tienen el espacio necesario.
Si el objetivo es rentabilizar el proceso de achaflanado, la decisión de utilizar el proceso de achaflanado mecánico es obvia. Los procesos mecánicos son inofensivos para la salud, económicos y prácticos. Se pueden ofrecer varias soluciones para espesores de chapa de 3 mm a 100 mm. El acabado varía. El chaflán creado en chaflanadoras por cizallado es muy preciso en términos de precisión angular, pero tiene una superficie rugosa, que es causada por la acción de la herramienta de corte. Sin embargo, este patrón rugoso no juega ningún papel en el proceso de soldadura posterior, ya que el material se funde completamente durante la soldadura.
Si el requisito del acabado final es alto, la fresadora portátil es una muy buena alternativa. Incluso se pueden procesar metales muy resistentes como Hardox y Duplex y se pueden crear chaflanes de hasta 60 mm de longitud.
La principal desventaja de las chaflanadoras es su alto grado de especialización, no pueden hacer otra cosa.